How to Identify and Repair Common Concrete Foundation Issues: A Homeowner’s Guide
Introduction
A strong foundation is vital for the stability and longevity of your home. Over time, concrete foundations can develop issues due to various factors such as soil movement, water damage, and aging. Identifying and addressing these problems promptly can prevent more serious damage and costly repairs. Here’s a guide to help homeowners recognize common concrete foundation issues and explore repair options.
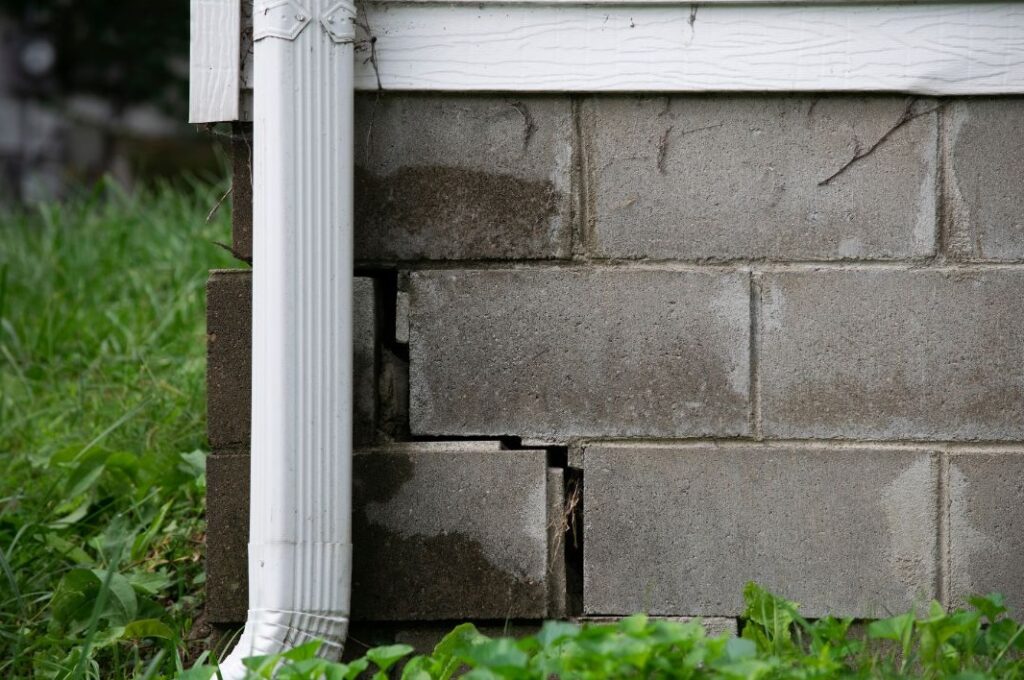
Identifying Common Foundation Issues
1. Cracks in the Foundation Walls
Symptoms: Visible cracks in the foundation walls can indicate underlying problems. Small, hairline cracks may not be serious, but larger cracks or those that change over time require attention.
Causes: Cracks can result from settling, thermal expansion, or pressure from soil and water. Structural issues can also contribute to crack formation.
2. Uneven or Sloping Floors
Symptoms: If you notice that floors are uneven or sloping, it may be a sign of foundation problems. Doors and windows that stick or are difficult to open can also indicate shifting.
Causes: Uneven floors often result from foundation settlement or poor soil conditions. Excessive moisture or soil erosion can also contribute to floor sloping.
3. Water Damage or Moisture Issues
Symptoms: Water damage or persistent moisture in the basement or crawl space can be a sign of foundation issues. Mold growth, dampness, or puddles are common indicators.
Causes: Water infiltration can occur due to poor drainage, leaky gutters, or foundation cracks. Excessive moisture can weaken the foundation and lead to further problems.
4. Bowing or Bulging Walls
Symptoms: Walls that bow inward or bulge outward can indicate significant foundation issues. This can be a serious problem requiring immediate attention.
Causes: Bowing walls are often caused by lateral pressure from soil or water. Poor drainage and expansive soils can contribute to this condition.
Repairing Foundation Issues
1. Crack Injection
Solution: For minor cracks, epoxy or polyurethane injections can be used to seal and stabilize the foundation. This method is effective for preventing water intrusion and reinforcing the crack.
Process: A professional will clean the crack, insert injection ports, and apply the sealant to fill the crack and restore structural integrity.
2. Piering and Underpinning
Solution: For more severe settlement or bowing issues, piering or underpinning techniques can be used to stabilize and support the foundation. This involves installing piers or supports beneath the foundation to transfer the load to more stable soil or bedrock.
Process: Professionals will assess the foundation’s condition, determine the appropriate piering method, and install the necessary supports to address settlement or shifting.
3. Drainage Solutions
Solution: Improving drainage around the foundation can prevent water-related issues. This may involve installing or repairing gutters, downspouts, and French drains to direct water away from the foundation.
Process: Proper drainage installation helps prevent future moisture problems and reduces the risk of foundation damage. Regular maintenance of drainage systems is also essential.
4. Wall Reinforcement
Solution: For bowing or bulging walls, reinforcement methods such as wall anchors or carbon fiber strips can be used to stabilize and strengthen the walls.
Process: A professional will assess the extent of wall movement, install reinforcement systems, and monitor the effectiveness of the repair.
Conclusion
Identifying and repairing concrete foundation issues early can save you from more extensive and costly repairs in the future. By understanding common problems and available solutions, homeowners can take proactive steps to maintain their home’s structural integrity. Consult with a foundation repair professional to assess your situation and recommend the best course of action.
For top-level concrete leveling and more, trust our expertise. Call us at 614-305-1050 for a free consultation, analysis, and estimate. Invest in the longevity of your home with our efficient and affordable waterproofing solutions.