Addressing Concrete Driveway Settling in Columbus, Ohio: Causes, Risks, and Repair Solutions
Introduction
A settled driveway is not only an eyesore but also a safety hazard. Over time, even a well-poured concrete driveway can settle due to various factors, leading to cracks, uneven surfaces, and potential trip hazards. This article will discuss the common causes of driveway settling, its risks, and the best solutions to restore your driveway.
What Causes Driveway Settling?
Several factors contribute to driveway settling, including:
- Poor soil compaction: If the soil underneath your driveway wasn’t compacted properly during installation, it can lead to settling as the ground shifts.
- Water infiltration: Poor drainage or water runoff can erode the soil under the concrete, causing it to sink.
- Tree roots: Nearby trees can cause the soil to shift as roots grow and expand.
- Heavy loads: Frequent exposure to heavy vehicles or machinery can compress the ground and cause the concrete to settle.
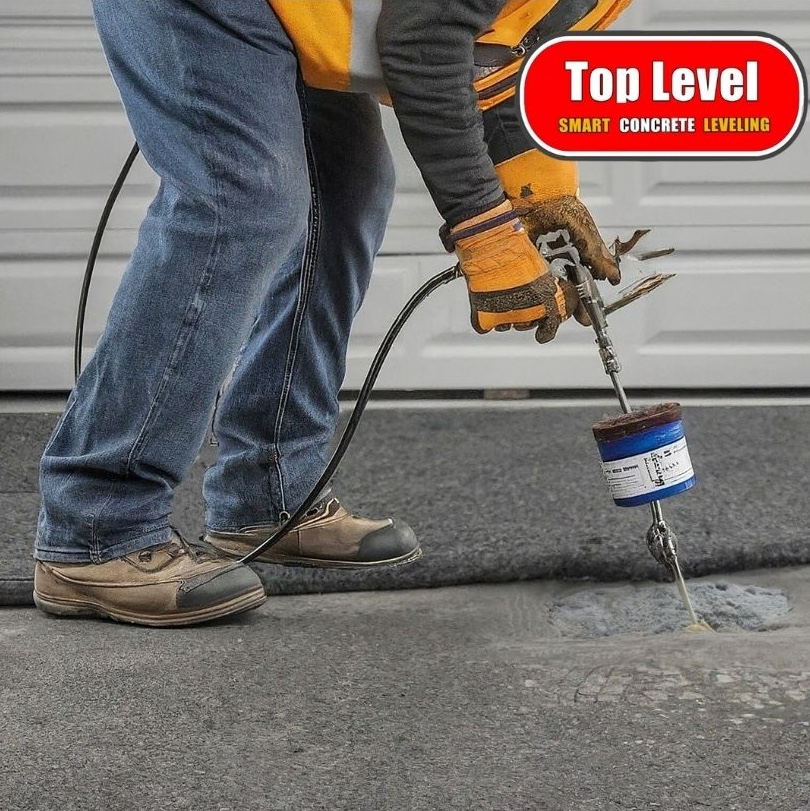
The Risks of Ignoring a Settled Driveway
A settled driveway poses several risks:
- Trip hazards: Uneven surfaces can cause accidents for pedestrians.
- Vehicle damage: Driving over a sunken driveway can strain tires and suspension systems.
- Water pooling: Sunken areas may cause water to pool, leading to further erosion and concrete deterioration.
The Best Solution: Polyurethane Foam Injection
At Top Level Ohio, we use polyurethane foam injection to address driveway settling. This cutting-edge method involves injecting high-density foam beneath the settled concrete, which expands and lifts the concrete back to its original level.
Benefits of Polyurethane Foam Injection:
- Fast and efficient: The foam expands quickly, allowing the driveway to be usable within hours after the repair.
- Durable: The foam is resistant to water, erosion, and extreme temperatures, ensuring a long-lasting solution.
- Non-invasive: Unlike other methods that require extensive digging or heavy equipment, foam injection involves minimal disruption to your property.
- Environmentally friendly: The polyurethane foam we use is eco-friendly and does not release harmful chemicals into the soil.
Preventing Future Settling
Once your driveway is repaired, it’s essential to take steps to prevent future settling:
- Ensure proper drainage: Divert water away from your driveway with well-designed drainage systems.
- Limit heavy loads: Avoid parking heavy vehicles on the driveway for extended periods.
- Maintain surrounding landscape: Keep trees and large plants away from the driveway to prevent root intrusion.
Conclusion
Concrete driveway settling is a common problem, but with the right repair techniques and preventative measures, you can restore your driveway and avoid future issues. Whether you choose foam injection or another method, addressing the problem early will save you time, money, and frustration.
At Top Level Ohio, we offer professional driveway leveling and repair services to homeowners in the Columbus, Ohio area. If you’re dealing with a settled or cracked driveway, our team specializes in polyurethane foam injection—a fast, durable solution that lifts and stabilizes concrete.
With our free consultation, detailed inspection, and tailored repair solutions, we can restore your driveway to its original condition, ensuring long-lasting results.
Call us today at 614-305-1050 to schedule your free estimate and get your driveway back in top shape!